1 Introduction
The ZSTZ15 gear grinding machine imported from Germany by our company in 1989 is the product of Germany's NILES company in the 1980s. Its control system takes PC603 and its I/O as its core, and the drive system's development, indexing, column, and tangential advancement. Both the DC drive and the DC servo motor were used for the grinding, and the ram stroke control was an electro-hydraulic servo drive. Due to the aging of electrical and hydraulic systems, PLC system often crashes, the failure rate increases year by year, the hydraulic servo system due to variable pump, servo cylinder, overflow valve and other components wear, the system's internal leakage and leakage are very serious, often due to pressure reduction It can not work, especially the Sanjiu and Davoo systems often fail. The stroke speed can only reach 40 times/minute due to the pressure reduction, which is only 2/3 of the original. The machine tool efficiency is greatly reduced, and the machining accuracy of the machine tool is also affected. Most of the gears processed are at level 10, which can no longer meet the needs of our company's production and development.
We have modified the NUM Axium Power 1050 digital control system from France to make this old device that has been working for nearly 20 years rejuvenated.
2. CNC transformation ideas
2.1 Numerical Control System
Using one of the most advanced all-digital numerical control systems in the world, the NUM Axium Power 1050G all-digital control system and its all-digital AC servo drive system produced by French NUM Corporation transform the original PC603 industrial control computer and its PLC system and its DC servo drive. The system is ideal for high-performance machine tools. The NUM Axium Power 1050 is a multi-processor CNC that processes and generates paths every 2 milliseconds and a 0.2 millisecond position loop refresh cycle. With a standard RS232 interface, 10.4-inch color LCD display.
2.2 Cancel Mechanical Hanging Wheel
The mechanical hanging wheels and the left and right tooth feed motors of the original machine tool were canceled. The generative motion and the left and right tooth face feed were replaced by the NUM CNC system and its all-digital AC servo drive system to control the X-axis and C-axis linkages. Using the dynamic operation function of the NUM system, the electronic hanging wheel is automatically generated through complex operations, the low-precision mechanical hanging wheel is eliminated, and the mechanical transmission link is reduced to ensure the accuracy of the exhibition movement relationship.
2.3 Develop friendly human interface
Development and design of gear parameter interface, grinding wheel parameter interface, dressing grinding and cycle grinding interface, through the man-machine interface can be easily modified gear parameters, process parameters. Automatic generation of related parameters such as stroke length, stroke speed, build length, and development speed simplifies the calculation and adjustment of various different specifications of gears before machining, simplifies operation, and improves machining efficiency.
2.4 Retrofit Stroke Hydraulic Servo System
The use of Germany Dr. servo valve and Rexroth variable displacement pump to update the transformation of the stroke hydraulic servo system, using the British NEWALL ball scale for stroke position feedback, so that ZSTZ15 gear grinding machine upgraded to a new CNC gear grinding machine.
2.5 Change the original column movement (Y axis), grinding wheel compensation (W axis) to NUM CNC system and its AC servo drive system control.
3. System hardware configuration
3.1 Numerical Control System
MUM Auium POWER 1050 with coprocessor GS
10.4†LCDcolor screen(FS20)
Industry QWERTY CNC keyboard(KBD30)
Machine panel(MP02)
Optical fiber 15m
OEM handwheel unit
3.2 The block diagram of the CNC system is as follows:
4. Software design
4.1 NC programming Use the unique dynamic operation function of NUM system to compile the program to generate the electronic hanging wheel to ensure accurate movement of the X-axis and C-axis to meet the tooth profile requirements of the cylindrical involute gear.
4.2 PLC programming Multi-task PLC program improves the writing and readability of PLC program. A total of %TS0 cyclic task module, %INI initialization task module and %SP1, %SP2, %SP3, %SP4, %SP5 are designed. , %SP6 six subroutine modules. The machine's start, enable, axis control, auxiliary functions, alarm information, etc. are compiled into different modules. The program structure is reasonable and the level is clear.
4.3 Man-machine interface design
Using MMITOOL software to develop a friendly manual interface, the main interface, gear parameter interface, dressing and grinding interface, grinding wheel interface, automatic circulation interface and alarm interface are designed.
4.3.1 Gear Parameters Interface
Figure 1 shows the gear parameter interface. The operator can automatically generate the display after inputting the relevant data (such as the number of teeth, modulus, helix angle, and tooth width, etc.) of the gear on the keyboard of the console in accordance with the gear processing drawings. The processing parameters such as process length, extension speed, stroke length, stroke speed, etc., can be processed without the need to prepare part programs. The operation is simple and reliable.
Figure 1 Parameter interface
According to the operator's experience, the automatically generated parameters can be adjusted to meet the processing needs.
4.3.2 Dressing and Polishing Interface
The dressing and grinding interface is a semi-automatic interface. In this interface, trial grinding can be performed on the aligned gears, and single tooth grinding and multi-tooth grinding can also be performed.
Figure 2 Dressing interface
4.3.3 Automatic Looping Interface
Fig. 3 is the automatic circulation interface, in which the grinding amount can be set and adjusted. Displays the number of machining cycles, the current machining status, gear parameters, the movement status of each axis, the current grinding amount, and the total grinding amount. It can control the oil temperature of the stroke hydraulic servo system.
Figure 3 automatic cycle interface
4.3.4 Manual Interface
Figure 4 manual interface
See figure 4. In the manual interface, the X axis, C axis, Y axis, W axis, and Z axis of the machine tool can be controlled independently. The equipped handwheel facilitates accurate tool setting. You can easily modify the stroke length, development speed, and the length of the generated length. The operator can directly input left and right tooth clearances based on experience to speed up the knife setting process.
4.3.5 Grinding Wheel Dressing Interface
Figure 5 grinding wheel dressing interface
The current diameter of the grinding wheel can be displayed on the dressing interface of the grinding wheel, and the dressing amount and the number of dressings can be input each time, and the current diameter of the grinding wheel can also be corrected.
4.3.6 Alarm Interface
Fault alarms appearing on the machine during operation are displayed on the screen to facilitate maintenance.
5. Stroke hydraulic servo system
Stroke hydraulic servo block diagram as shown below:
6. Conclusion
The NUM Axium Power 1050 all-digital control system is well known in the world for military and aerospace industry applications in Europe and the United States. It is one of the most advanced all-digital numerical control systems in the world. It was applied in the CNC transformation of the ZSTZ15 gear grinding machine. Not only has the production efficiency been nearly doubled, but also the machining accuracy of machine tools has been improved, the income of operators has been increased, and significant economic benefits have been generated. Inaugurated the use of the NUM system to replace the mechanical rolling wheel model to transform the first large-scale gear grinding machine, made a breakthrough in the gear machine transformation.
Metal Crushing Machine, also known as scrap Metal Crusher machine, this equipment is to crush the waste metals by applying the impact and shear force and even some grinding force, after processing with the scrap metal crusher, the output size usually small iron balls, which is with bigger density, as the volume is largely reduced, then it can be conveniently stored, transported to the smelting factory for casting into plates, ingot, rod and so on. A complete scrap metal crushing system(waste metal recycling plant) mainly consists of belt conveyors, metal crusher, Dust Collector to prevent the dust from entering the factory and the panel control system.
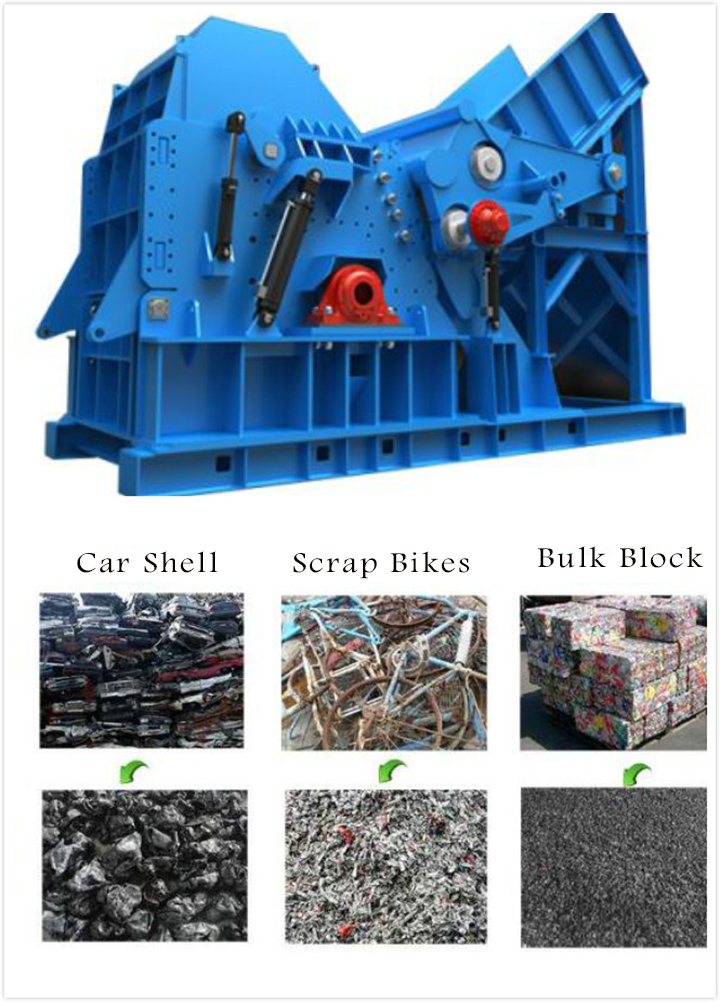
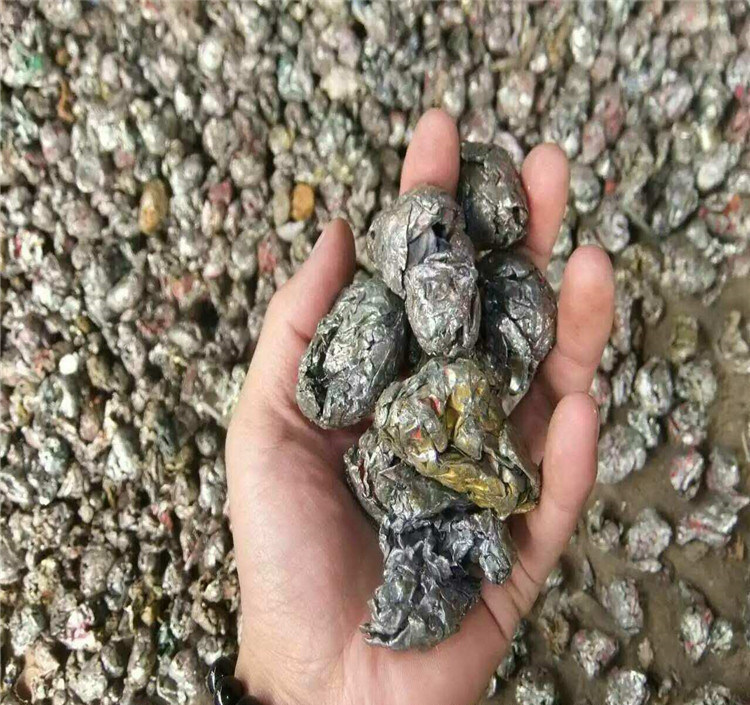
Metal Crusher
Metal Crusher,Metal Crusher Machine,Undertale Metal Crusher,Metal Scrap Crusher
Henan Mingyuan Heavy Industrial Machinery Company Co., LTD. , https://www.heavyequipment-china.com